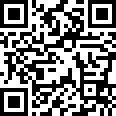
Ms. Jewel
Leave a messageMs. Jewel
Leave a messagecnc machining of general curved parts usually uses ball end mills. When the ball end milling cutter is used to machine the curved surface, the cutting process is performed by the line cutting method, that is, the milling cutter processes the curved surface line by line along the coordinate axis direction or the parameter axis direction. After each line is processed, the milling cutter moves a line spacing until the entire surface is finished. . The size of the line spacing of the cutting point directly affects the machining accuracy and machining efficiency of the surface. A line spacing value less than the actual cutting width will increase the machining time and also result in a decrease in programming efficiency and a program expansion. When the line spacing value is larger than the actual cutting width of the tool, the surface residual ridge height of the curved surface is increased, so that the surface roughness value and the error are increased.
First, the curved three-axis Cnc Machining line cutting method analysis 1. Surface three-axis CNC Machining line cutting method produces the residual ridge height when the surface is cut by the ball-end milling cutter, it will leave a relatively obvious on the machined surface. Scallop height.
(1) Analysis of the height of the residual curved surface of the convex surface For a convex curved surface, a, b, and g are the tool points. The radius of curvature of point a or b can be approximated as a circle. The height of the residual ridge is analyzed as follows: H=of-fc -od H is the height of the residual ridge, r is the radius of the tool, S is the cutting line spacing, and R is the radius of curvature of the surface.
It can be seen from the above analysis that the height of the residual ridge is determined by the tool radius r and the cutting line spacing S. The larger the tool radius r is, the smaller the residual ridge height is; the smaller the cutting line spacing S is, the smaller the residual ridge height is as shown. However, the cutting line spacing S is small, which increases the number of passes and increases the amount of program. The height of the residual ridge affects the machining accuracy and surface roughness of the surface.
(2) Analysis of the height of the residual curved surface of the concave surface For the concave curved surface, a, b, and g are the tool points. The radius of curvature of point a or b can be approximated as a circle. The height of the residual ridge is analyzed as follows: From the above analysis, it can be known that: The height of the residual ridge is determined by the tool radius r and the cutting line spacing S. The larger the tool radius r is, the smaller the residual ridge height is. The smaller the cutting line spacing S is, the smaller the residual ridge height is, but the cutting line spacing S is smaller and the number of passes is increased. The amount of program increases. The height of the residual ridge affects the machining accuracy and surface roughness of the surface.
Because it is obvious that for the concave and convex curved surface with the same radius of curvature, under the condition that the tool radius and the line spacing are equal, the height of the residual ridge generated by machining the concave curved surface is larger than the height of the residual ridge generated by the curved surface.
2. Interference error generated by curved three-axis NC machining line cutting method When the three-axis machining surface is machined, the tool contact is the actual contact point between the tool and the workpiece during the machining process, which produces the final cutting effect, and the tool position is the tool. The coordinate point of the programmed position, so the tool position produces a theoretical tool path, and the path generated by the tool contact has an error with the path generated by the tool point. The δ1 and δ2 in the middle are called interference errors. The magnitude of the interference error is related to the cut-in and cut-out position and the tool radius during machining. In the middle, the interference errors δ1 and δ2 generated by the line spacing ab and bg segments are related to the angle between the line spacing segment and the XY plane, the angle between the line spacing segment and the XY plane is 0, and the interference error is the smallest, so δ2 is larger than δ1. The error is large.
3. MasterCAM-based three-axis surface processing line spacing control is based on the surface streamline processing (Flowline). Streamline processing refers to machining along the streamline direction during machining to create a tool path at a certain interval until the entire surface is taken. There are two ways to determine the distance between the cutting paths. The Distance and Scallopheight.Distance set the distance between each cutting path, which is generally used for roughing.
The Scallop height sets the height of the residual material left between the cutting paths. The distance between the cutting paths is automatically adjusted by the system. Because the same residual material height is set, the distance between the curvatures of the surface during processing is large. The surface curvature is small where the curvature of the surface is small, and it is used for finishing and semi-finishing.
Second, the surface five-axis CNC machining line cutting method analysis 1. Surface five-axis CNC machining line cutting method generated residual ridge height with a ball-end milling cutter for the surface of the five-axis line cutting process, will also leave a section on the machined surface The apparent height of the residual ridge (Scallop height), the height of the residual ridge is determined by the tool radius r and the cutting line spacing S. The larger the tool radius r is, the smaller the height of the residual ridge is. The smaller the cutting line spacing S is, the smaller the height of the residual ridge is. As shown. However, the cutting distance S is small, and the number of passes is increased, and the program amount is increased. The height of the residual ridge affects the machining accuracy and surface roughness of the surface.
When the surface is machined by five axes, the tool contact and the tool point are the same point, and the track generated by the tool contact coincides with the track generated by the tool point, so there is no interference error.
(1) Analysis of the height of the residual curved surface of the convex surface As shown, for convex curved surfaces, a and b are the tool points, and the radius of curvature of point a or b can be approximated as a circle. The height of the residual ridge is analyzed as follows: H=of -fc-R fc= 2 1 rof? Where H is the height of the residual ridge, r is the radius of the tool, and S is the cutting line spacing, which is the radius of curvature of the R surface.
(2) Analysis of the height of the residual curved surface of the concave surface For the concave curved surface, a and b are the tool points, and the radius of curvature of point a or b can be approximated as a circle. The height of the residual ridge is analyzed as follows: H=od-of-fc Oo 1 =Rr o 1 f= 2()4 R r, obviously for the concave and convex surface with the same radius of curvature, under the condition that the tool radius and the line spacing are equal, the height of the residual ridge generated by the concave surface is higher than that caused by the convex surface. The ridge height is small.
2. The line spacing control of the five-axis surface machining based on MasterCAM is based on the five-axis surface streamline processing (Flow5ax).
As shown, streamline machining refers to machining along the streamline direction during machining, creating a single tool path at a certain interval until the entire surface is taken. Select Flow5ax processing, the system pops up the dialog box, select 5-axis machining (5 Axis), select the pattern sample (Pattern Suface), the system returns to the drawing work area, select the surface, and determine. Enter the "Flow 5ax parameters" setting, as shown in Figure 1, the Stepover control settings determine the distance between the cutting paths. There are two ways to calculate the distance between each cutting path, that is, Distance and Scallop height. Distance set the distance between each cutting path, generally used for roughing. The Scallop height is used to set the distance between the cutting paths and the distance between the cutting paths is automatically adjusted by the system for finishing.
Third, the conclusion is as shown, the same line spacing, five-axis surface processing is slightly higher than the residual ridge height generated by the three-axis machining, but the five-axis surface processing does not produce interference error, and the three-axis machining produces interference error. Moreover, by appropriately increasing the tool radius, the height of the residual ridge of the five-axis surface machining can be reduced, but the height of the three-axis machining residual ridge is reduced and the interference error is increased rapidly.
Privacy statement: Your privacy is very important to Us. Our company promises not to disclose your personal information to any external company with out your explicit permission.
Fill in more information so that we can get in touch with you faster
Privacy statement: Your privacy is very important to Us. Our company promises not to disclose your personal information to any external company with out your explicit permission.